AI-Driven Safety Revolution: Empowering a Global Beverage Leader to Achieve Zero Incidents [Success story]
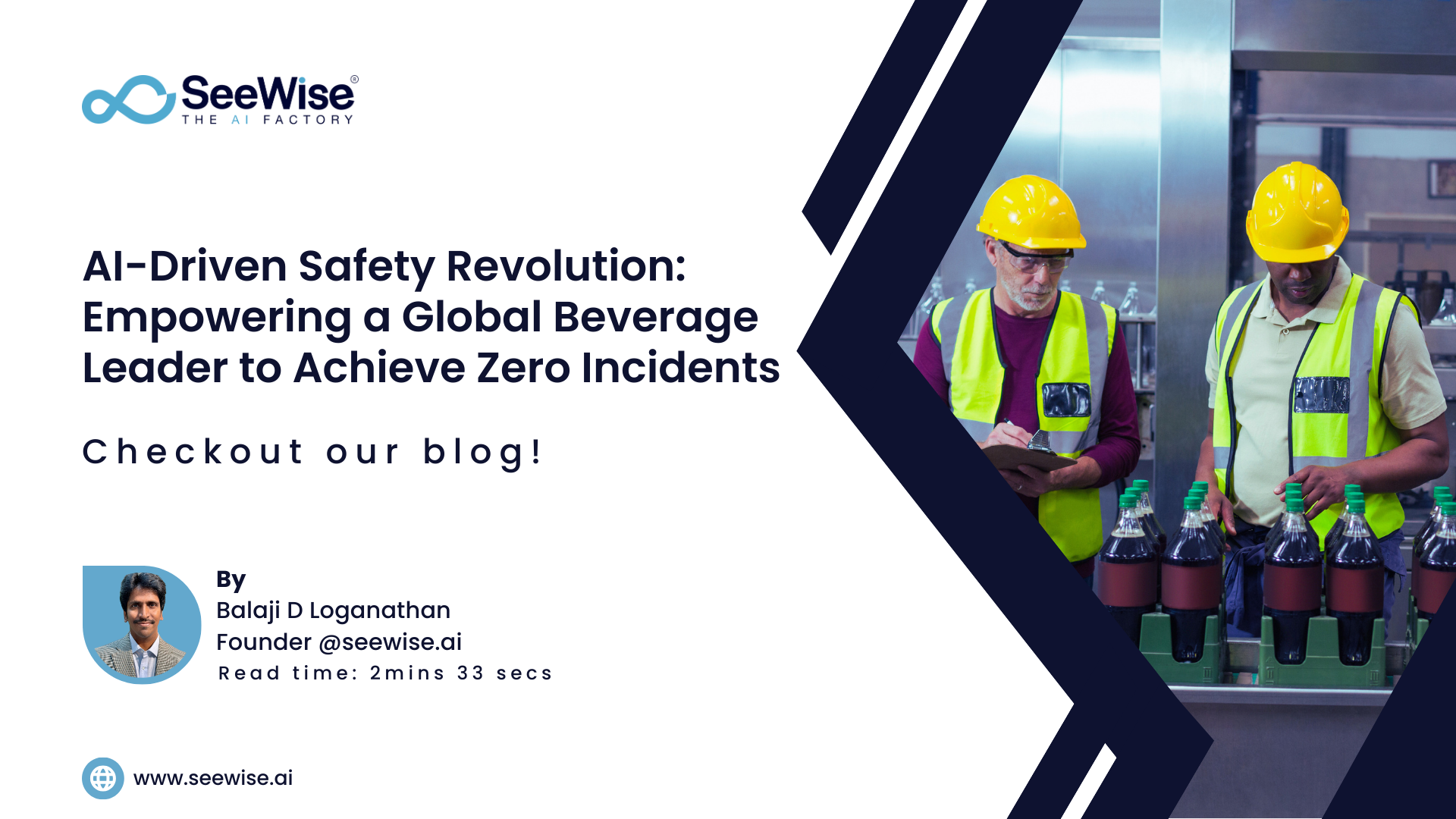
Abstract
In a fast-paced manufacturing environment, safety isn’t just a priority, its a necessity. Discover how Seewise’s Vision AI, powered by INTEL'S OpenVINO toolkit, transformed safety protocols at a global beverage giant. By integrating real-time human presence monitoring with PLC/SCADA systems, the solution slashed risks, achieved near-zero incidents, and redefined compliance
Introduction
In environments where humans and machines operate side by side , even a split-second lapse can lead to violations. Beverage manufacturing plants, with their palletizers and high-speed wrappers, face unique challenges. Traditional safety measures reliant on manual checks or physical barriers often leads to failure in dynamic environments.
Enter seewise’s vision ai , a system that merges cutting-edge computer vision with INTEL'S OpenVINO-optimized ai models to detect, predict, and prevent safety breaches. This success story dives into how the solution turned a leading manufacturer’s safety goals into reality.
Challenges in Modern Manufacturing
Manufacturing plants face the following safety challenges:
- Unsafe Zone Entries:Workers stepping into active machine zone leads unexpected accidents.
- Human Oversight Gaps: Missed incidents due to human error and causing a major setback.
- Inefficient Response Mechanisms:: Existing mechanisms lag between detection and machine shutdown.
- Compliance and Accountability: Difficulty in tracking and maintaining adherence to safety protocols.
The Seewise Solution: Vision AI meets INTEL'S OPENVINO
Core Features
Seewise's vision-based system combined AI precision with industrial grade reliability, Let’s see how it worked:
- Real-Time Human Detection: : Using OpenVINO-optimized models analyzed human presence in restricted zones near active machines.
- Automated Machine Stoppage: Instant plc integration will trigger the machine to shutdown with in a sec of a violation
- Smart Alerts: Audible alarms, sms/email alerts will be triggered instantly in real time. Ensuring safety.
- Dashboard Insights: Provides dashboards showcasing safety compliance scores, violation trends, and spatial analytics.
- Scalable Architecture: Built on INTEL'S edge computing infrastructure which ensured low-latency processing 24/7 in all kinds of environments.
Why OpenVINO?
- Optimized Performance:OpenVINO’s model compression and hardware acceleration slashed inference times and ensured 2x performance than the existing model inference.
- Seamless Integration: OpenVINO toolkit ensures seamless integration with their api ensuring minimal configuration and making integration much faster
Integration with Existing Systems
- Hardware: High-resolution CCTV IP cameras deployed strategically near critical machinery
- Software: AI models trained to recognize human presence with 95%+ accuracy after on-site calibration.
- OpenVINO™ Toolkit:: Used to optimize deep learning models for high-performance inference on edge devices, and INTEL based systems, ensuring real-time safety alerts.
- PLC Communication: Bi-directional communication with controllers to stop or restart machines based on detected activity.
Implementation Workflow
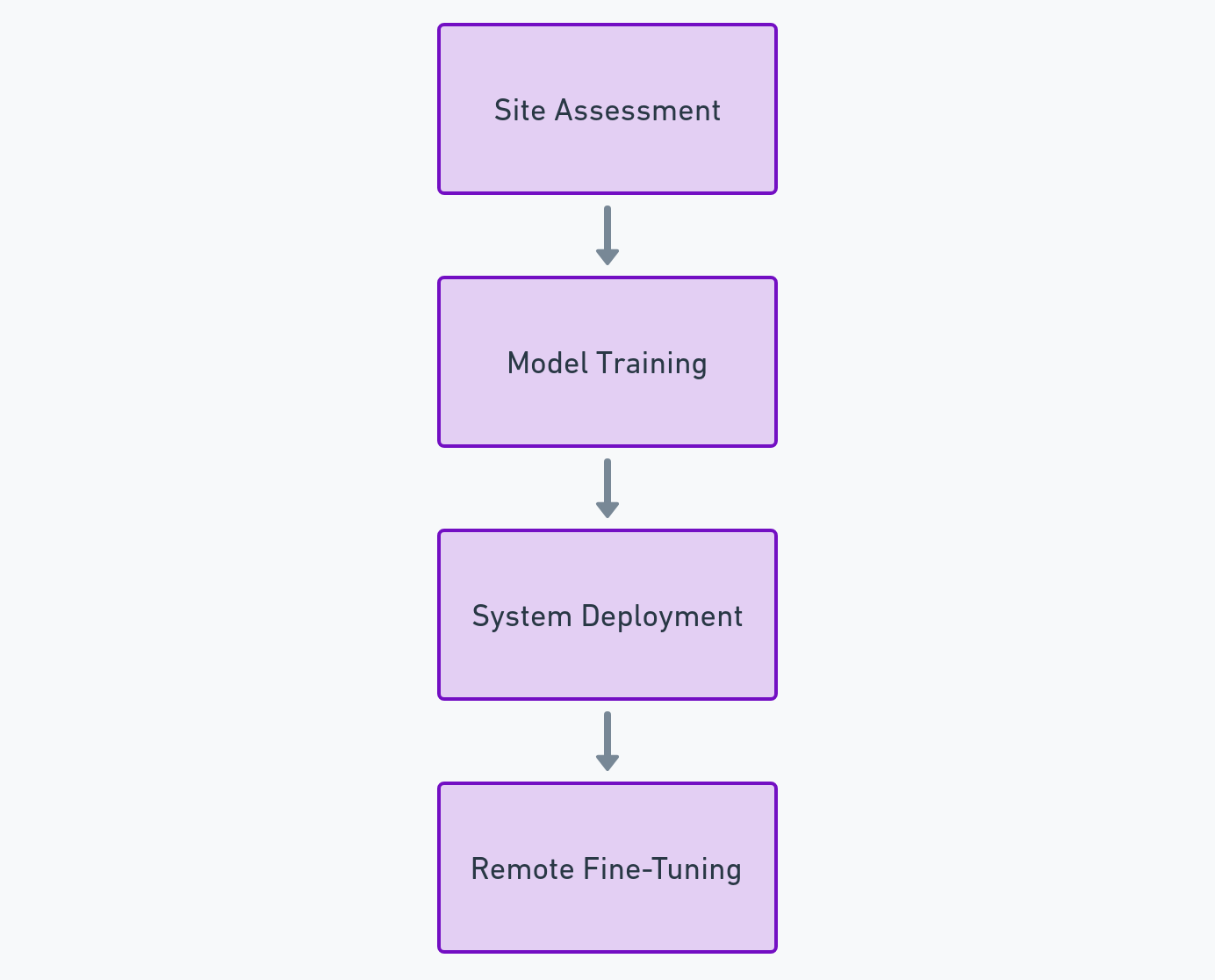
- Site Assessment: Determine optimal camera placement and system integration points.
- Model Training: Collect and label video data from the site to train AI models.
- System Deployment: Install hardware and software, ensuring seamless communication with on-premise PLCs.
- Remote Fine-Tuning: Continuously improve model accuracy with live data during the pilot phase.
- User Acceptance Testing (UAT): Validate performance with the client’s safety and operations teams.
Impact and Outcomes
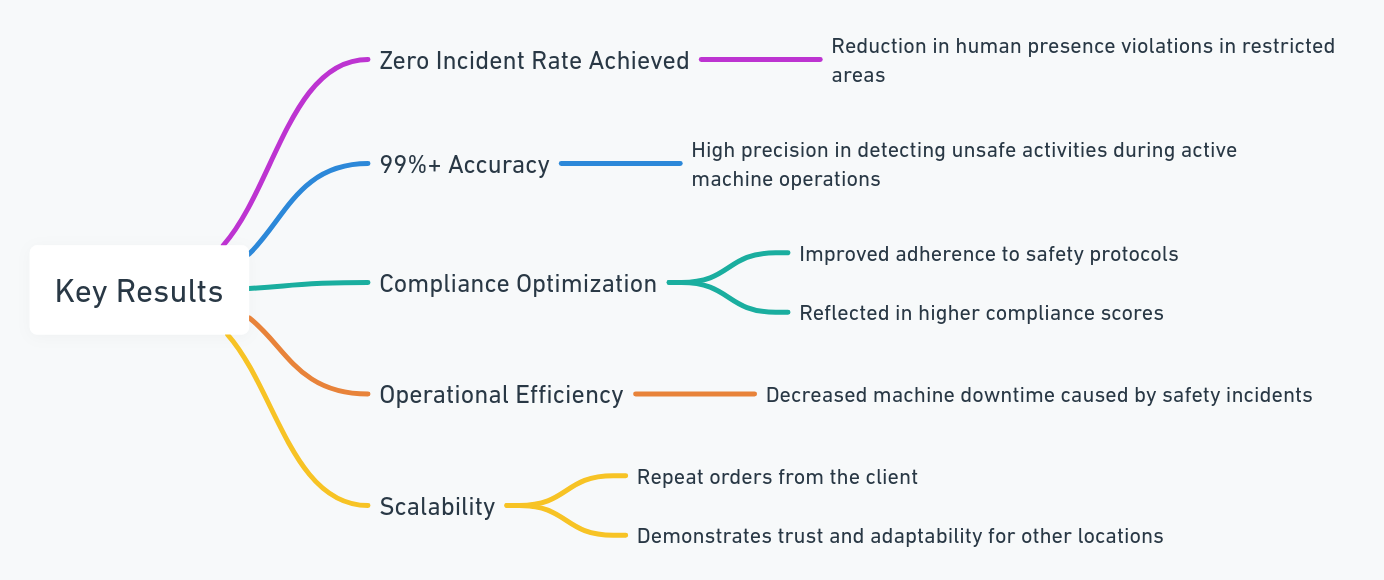
Key Results
- Zero Incident Rate Achieved: Reduction in human presence violations in restricted areas.
- 99%+ Accuracy: High precision in detecting unsafe activities during active machine operations.
- Compliance Optimization: Improved adherence to safety protocols, reflected in higher compliance scores.
- Operational Efficiency: Decreased machine downtime caused by safety incidents.
- Scalability: Repeat orders from the client demonstrate trust and the system's adaptability for other locations.
ROI and Long-Term Value
- Cost Savings:Reduced liability from workplace accidents and machine downtime.
- Safety Culture: A data-backed safety-first environment, reinforcing employee trust and regulatory compliance
- Future-Ready Platform: The AI model’s adaptability allows expansion to other processes and facilities.
Replicating Success Across Industries
Seewise’s LVM (Large Vision Model) solution has proven its potential to create safer work environments in high-risk, high-output industries. Its modular design ensures seamless customization for sectors like automotive, FMCG, logistics, and beyond. The system's core functionalities can be tailored to suit diverse operational needs, enabling scalable adoption.With the additional optimization provided by the OpenVINO™ toolkit, the solution delivers unparalleled inference speed and scalability.