Reigniting Growth in India’s Foundries: Harnessing AI to Tackle Challenges and Drive Profitability
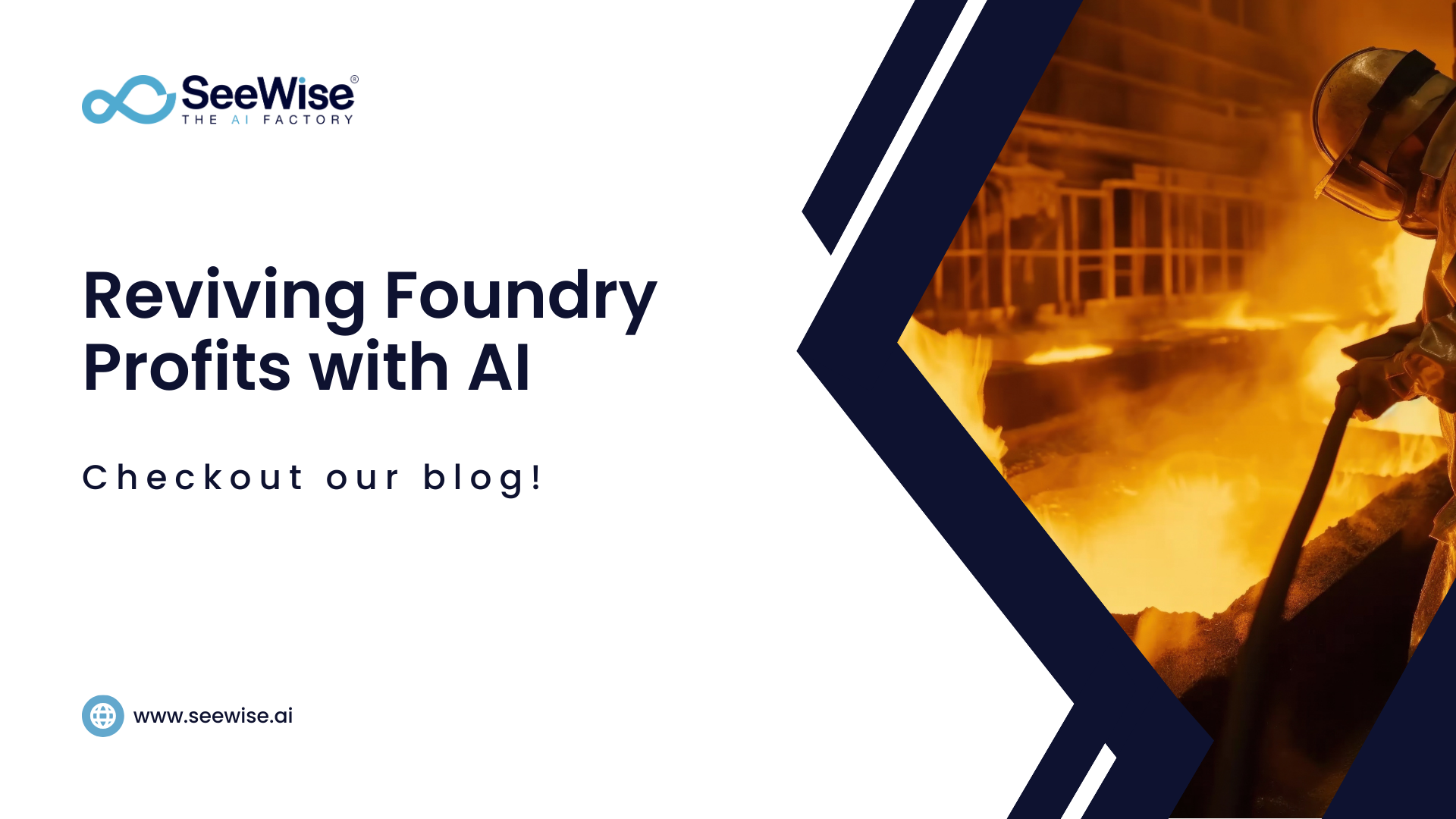
As National Foundry Day approaches, it’s a crucial time for industry leaders to reflect on both the successes and the challenges faced by India’s foundries. India has emerged as the world’s second-largest producer of castings, surpassing the United States and trailing only China. This achievement highlights the strength of India’s manufacturing capabilities. However, alongside this growth lies a set of challenges that, if unaddressed, could hinder future progress. Among these, declining furnace efficiency and rising energy costs are significant issues. The answer to these challenges may lie in leveraging advanced technologies, particularly AI in furnace monitoring, to revitalize the sector and ensure sustained profitability.
India’s Foundry Industry: Growth Amid Challenges
The foundry industry in India has long been a cornerstone of its manufacturing ecosystem, producing essential components for automotive, aerospace, construction, and heavy machinery sectors. Despite its scale, the industry is currently under pressure from various angles, including high operational costs, environmental regulations, and the inefficiency of traditional furnace systems.
India’s position as a global leader in casting production is at risk if these issues are not addressed. Foundries operate with narrow profit margins, and inefficiencies in furnace operations can quickly erode these margins. The foundries energy-intensive nature, coupled with the aging furnace infrastructure, often results in increased wastage, downtime, and reduced output quality.
The Role of AI in Furnace Monitoring
One of the most promising advancements in overcoming these challenges is the integration of AI into furnace monitoring systems. AI-driven solutions, particularly those based on computer vision, are uniquely positioned to address inefficiencies in furnace operations, ensuring consistent output and improved resource management.
Here’s how AI in furnace monitoring can make a significant impact:
- Real-time Process Optimization: AI-based systems can monitor furnace operations in real time, analyzing vast amounts of data from heat, temperature patterns, and material properties. By providing actionable insights, these systems help fine-tune the furnace parameters dynamically, resulting in more precise melting processes. This leads to a consistent casting quality, which is crucial for meeting stringent industry standards
- Energy Management:One of the biggest concerns in foundry operations is the high energy consumption of furnaces. AI solutions can optimize energy usage by analyzing the furnace’s thermal behavior and identifying areas where energy is being wasted. For instance, computer vision systems can detect subtle temperature variations and optimize the energy input to maintain the desired melting point with minimal wastage. By doing so, foundries can significantly reduce their energy bills while also contributing to sustainability goals.
- Reducing Downtime:Downtime in furnace operations is costly and often arises from manual monitoring inefficiencies or delayed detection of faults. AI-powered computer vision systems can continuously monitor furnaces, detecting anomalies such as slag formation, inconsistent heat distribution, or material flow issues that might lead to unplanned shutdowns. Early detection and real-time alerts allow operators to take corrective actions promptly, reducing downtime and maintaining production flow.
- Improving Product Quality:The quality of the final casting is heavily dependent on how well the furnace is managed during the melting process. AI in furnace monitoring offers detailed insights into the conditions within the furnace, ensuring that critical factors such as temperature, material composition, and timing are all within optimal ranges. This minimizes defects, reduces rework, and enhances overall product quality. Higher consistency in output also builds trust with clients, leading to stronger market positioning.
- Sustainability and Environmental Compliance:Environmental regulations are becoming increasingly stringent, and foundries must adapt to these changing norms. AI-driven furnace monitoring helps optimize resource usage, reducing both waste and emissions. Additionally, data collected through AI systems can be used to demonstrate compliance with environmental standards, which is increasingly demanded by global clients.
Case Study: AI Adoption in a Leading Indian Foundry
To illustrate the tangible benefits, consider a leading Indian foundry that recently adopted an AI-based furnace monitoring system powered by computer vision. Before implementing AI, the foundry faced frequent production halts due to inconsistent furnace performance, leading to high scrap rates and energy waste.
Post-implementation, the foundry reported a 20% reduction in energy consumption and a 15% improvement in casting yield. The AI system provided real-time insights, allowing operators to make data-driven decisions, thus enhancing operational efficiency. By minimizing human error and automating critical monitoring tasks, the foundry also saw a significant reduction in downtime.
A Path Forward: Embracing AI for Sustainable Growth
As India’s foundry sector faces the dual pressures of maintaining its competitive edge while adapting to changing economic and environmental landscapes, the adoption of AI in furnace monitoring presents a clear path forward. The technology not only addresses immediate operational challenges but also positions foundries to thrive in the future.
To sustain their growth and avoid the pitfalls of declining furnace performance, foundries need to focus on reducing energy wastage and minimizing downtime. AI solutions, particularly those that leverage computer vision for real-time monitoring and optimization, offer a strategic advantage by delivering consistent results and enhancing overall productivity. By embracing these technologies, foundries can ensure they remain resilient, profitable, and globally competitive.
As National Foundry Day reminds us of the industry’s significance, it also serves as a call to action for leaders to invest in the future. The integration of AI into furnace monitoring is no longer just a technological upgrade—it’s a necessity for sustaining growth, driving profitability, and securing India’s position as a global leader in the foundry industry.